紙の使用量年間18,000枚/年削減!kintone x トヨクモkintone連携サービスによる、製造現場のDX推進事例
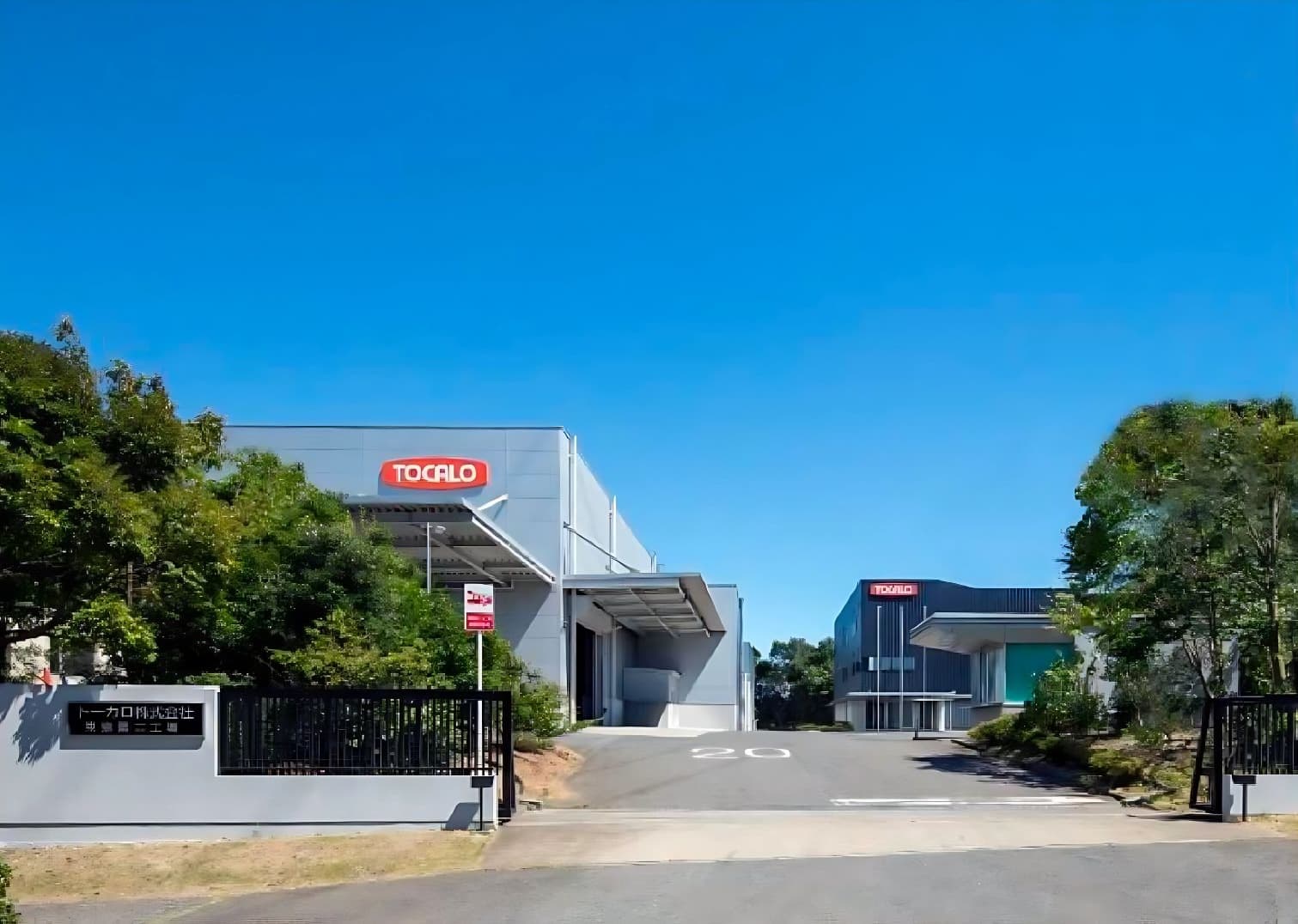
表面改質技術のリーディングカンパニーとして、創業以来70年以上にわたり、溶射加工をはじめとする最先端の技術を保有するトーカロ株式会社。電力や鉄鋼、自動車などの基幹産業から、宇宙開発、先端医療に至るまで、幅広い分野で付加価値を提供しています。
同社は、kintoneとトヨクモkintone連携サービスの導入を通じて、紙ベースだった加工指令書の電子化や、測定機器管理の大幅な効率化に成功。現場視点でDXを推進させ、紙の使用量を年間18,000枚削減しています。
本記事では、トーカロ株式会社 東京工場 鈴身事業所 製造1部 溶射3課 岩崎晃子様、上野有史様に、トヨクモkintone連携サービスの具体的な活用事例と、導入効果についてお話を伺いました。
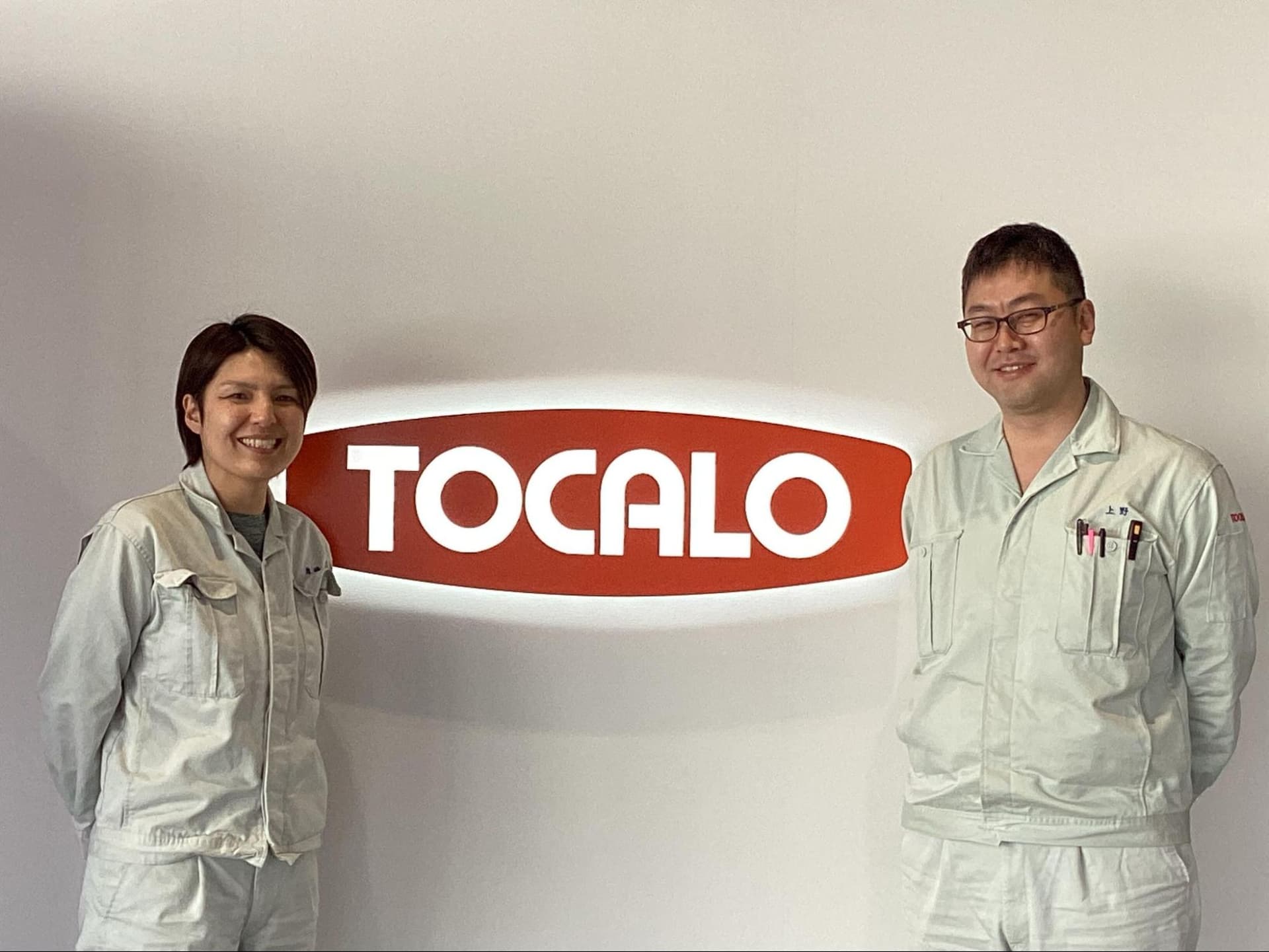
製造現場を圧迫していたアナログな承認フローや連絡手段の見直しへ
同社では、これまで紙の加工指令書を用いて精密部品の製造プロセスを管理していました。加工指令書には必要な工具や作業手順が記載されているため、作業を開始するにあたって欠かせない存在です。
しかし、紙の指令書にはいくつかの課題がありました。まず、承認者の不在による回覧漏れです。承認フローが完了するまでに1週間以上かかることもあり、工具の手配や加工工程が後手に回り、スケジュール全体に影響を及ぼしていました。
「承認フローだけでなく、生産状況の進捗共有にも問題がありました。共有方法がメールや電話など個人間のやり取りに依存していたため、製品の進捗や施工保留の原因をすぐに把握できないことが多かったのです。また、状況を把握している担当者を探し回る必要があり、聞いても別の担当者を案内されることが頻発していました。こうした状況が月に200~300件の製品で繰り返され、業務効率の低下を招いていました」(岩崎氏)
そこで、展示会の視察やインターネット検索などを通じて、工程管理における業務改善に向けた情報収集を開始。しかし、“お客様の要望に応じた多品種少量生産”を強みとする同社の特性上、既存システムでは適したものが見つからなかったそうです。
その後、パートナー会社と打ち合わせを重ね、半年の準備期間を経てkintoneとPrintCreatorを導入。kintoneは、プログラミングの知識がなくてもアプリを構築できる柔軟性があり、業務への適応しやすさが決め手となりました。また、デジタル化による現場の混乱を抑えるため、従来の紙の加工指令書と同じフォーマットを再現でき、電子承認印に対応したPrintCreatorを導入し、スムーズな移行を実現しました。
kintoneとPrintCreatorの導入にあたり、「取り残されたと感じる社員が出ないよう配慮したことがよかった」と岩崎氏は振り返ります。
「新しいシステムに抵抗を感じる社員が出ないよう、事前に1人1台のiPadを支給しました。ただ配るだけではなく、画面にはフィルムを貼り、保護ケースに入れ、kintoneがすぐ立ち上がるように設定を済ませた上で、一人ひとりに手渡ししながら説明しました。
また、いきなり紙の加工指令書を廃止するのではなく、2カ月ほどの移行期間を設け、従来の方法と並行しながらkintoneに慣れる時間を確保しました。その結果、従業員からの反発はなく、むしろ自発的に活用する声が聞かれるようになり、スムーズな導入につながったと感じています」(岩崎氏)
紙の使用量を年間18,000枚削減!納期遅延も解消したトヨクモkintone連携サービス活用事例
加工指令書(PrintCreator)
従来は、製品に関する情報を確認できるよう、紙の加工指令書を製品に貼付していました。しかし、加工指令書の電子化に伴い、「製品の情報にアクセスしづらい」という現場の声が上がったのです。そこで、PrintCreatorを活用し、客先品名や加工指令書ページと連携するQRコードを発行。製品に貼付することで、その場でスムーズに情報を確認できるよう改善しました。
▲PrintCreatorで発行したQRコードが加工中の製品に貼付されている様子
さらに、コメント機能を活用した情報共有により、これまで統一されていなかった連絡手段が一元化され、レコードを開けば、いつでも誰でも進捗が分かるようになりました。その結果、作業効率が向上し、現在では「kintoneのコメントに載せておきます」といった、社員の自発的な活用も広がっています。
また、ペーパーレスの効果は高く、紙の使用量は、月1,500枚(年間18,000枚)削減を実現しました。
「目に見えるペーパーレス化などの成果に加え、従業員からの評価が得られているのも嬉しいポイントです。作業現場では、承認待ちによるタイムロスが解消され、工具の事前手配が可能になったことで待ち時間が短縮。工程計画の精度が向上し、作業効率が改善しました。その結果、営業部門からも納期遅延のリスクが回避されたと評価されています」(上野氏)
測定機器管理システムの構築(PrintCreator)
加工後の製品寸法検査に使用する測定機器の管理にも、kintoneとPrintCreatorを活用しています。
従来は測定機器の精度を保証するため、年に一度実施する外部委託校正の前に対象機器の状態確認とリストアップに膨大な時間を要していました。その結果は、エクセルで台帳管理していましたが、校正対象の設備は約1,500件に及び大きな負担となっていました。
そこで、kintoneを活用し、測定機器の管理をアプリ化。さらに、PrintCreatorで発行したQRコードを各測定器に貼付し、現場でコードを読み込むだけで、リアルタイムに情報を更新できる仕組みを構築しました。これにより、検索の手間が大幅に削減され、管理の精度が向上。従来は複数名で対応していた故障対応等の運用管理も、管理者1名で対応できるようになりました。
▲測定機器管理アプリ
▲PrintCreatorで発行したQRコードが測定機器に貼付されている様子
さらに、測定機器の使用頻度が可視化されたことで、稼働率に応じた適正な保有台数を管理できるようになり、更新計画も定量的に立案できるようになりました。その結果、維持コストを100万円単位で削減することに成功しています。
▲加工指令書アプリには使用測定機器の入力欄があり、製品ごとの測定記録が残せるようになっている
「製造業の品質管理において、信頼性を担保するためのISO 9001という国際規格があります。この規格では、計測器の校正時の動作確認に加え、その結果や実施担当者の記録を保管することが求められます。従来の体制では対応方法に苦慮していましたが、kintoneとPrintCreatorの導入により、ISOに適した記録が可能になりました。
校正記録の体制が整ったことで、お客様の要望に応じた校正結果報告書をスムーズに出力できるようになりました。この品質管理の取り組みはお客様からも好評で、関心を持ったお客様には同様の仕組みの導入を勧めています」(上野氏)
業務改善の取り組みはまだ道半ば。これからも品質・効率向上を目指す
2024年8月に、kBackupを導入した同社。その背景には、kintone内のデータを誤って削除してしまうトラブルがあったそうです。最終的には復旧できたものの、完了までには時間と労力がかかり、大きな負担となりました。kBackupを活用してからは、登録されたデータや添付ファイルを自動でバックアップできるようになり、情報の消失リスクが大幅に低減しました。
着実に業務改善を進める同社ですが、「まだやるべきことは多い」と上野氏は話します。特に今後は、社内のナレッジ共有の強化と個人情報の管理に力を入れていく考えです。
「当社は専門性の高い事業を手がけており、インターネットやAIでは得られない知見が多くあります。試験結果や開発の過程は貴重な情報資産なので、個人の中に埋もれさせるのではなく、全社で共有できる仕組みを整えたいと考えています」(上野氏)
また、工場に出入りする作業者の個人情報管理も重要な課題となっています。
「お客様の工場で作業を行う一部の部署や協力業者は、入場時に緊急連絡先などの個人情報を提出する必要があります。しかし、取得した情報はすぐに破棄しなければならず、年間100回以上の情報収集作業が大きな負担となっていました。そこで、FormBridgeを活用し、個人情報の収集をWebフォームで一元化するとともに、登録済みの内容を本人が確認できる仕組みの構築を検討しています」(上野氏)
最後に、岩崎氏は今後の展望について次のように語ります。
「kintone導入にあたり、指示書アプリの電子化と工程管理の最適化を進めたいと考えていました。指示書アプリの電子化はすでに実現完了。次のステップとして、製品の作業予定や実施状況をkintone上で一元管理できるよう、準備を進めています」(岩崎氏)